מטרת הציפוי
אחת הסיבות העיקריות שבגללן אנו מצפים מתכות, היא כדי ליצור שכבת הגנה ולמנוע התפתחות קורוזיה בחומר הגלם שלנו. התפתחות קורוזיה מקצרת את אורך חיי המוצר, פוגעת בתכונות הפיסיקליות ובנראות של המוצר. קיימות סיבות נוספות לביצוע תהליך צביעה או ציפוי, כגון:
- שיפור עמידות בשחיקה – לדוגמה אבץ ברזל.
- בידוד חשמלי – לדוגמה אנודייז.
- מוליכות חשמלית – לדוגמה כסף.
- הגדלת הרפלקטיביות – לדוגמה אלקטרולס ניקל.
- דקורטיביות – לדוגמה זהב.
בעת בחירת הצבע או הציפוי יש להתחשב במספר גורמים, כגון: חומר הגלם, תנאי האחסון נדרשים וכדאיות כלכלית.
הגדרות:
1. קורוזיה (שיתוך) (Corrosion)
קורוזיה זה תהליך אלקטרוכימי המתקיים על פני שטח המתכת, במהלכו נקשרת המתכת לחמצן שבאוויר והופכת ל”תחמוצת ברזל” – “חלודה”. התהליך מתרחש בסביבה לחה. תהליך התפתחות הקורוזיה כולל את המתכת (אנודה וקתודה), האלקטרוליט (תמיסה/לחות באוויר), ואת המוליך/קשר בין המתכות. למניעת קורוזיה עלינו לדאוג למעטפת הגנה חיצונית.
2. קורוזיה גלוונית (Galvanic corrosion)
סוג של קורוזיה אשר נפוץ בתעשייה, הנגרמת כתוצאה מתכנון שגוי של צימוד חומרים (מגע בין שני חומרים). אם נבחרו שתי מתכות אשר לפי השורה (טבלה) הגלוונית, הפוטנציאל האלקטרוכימי ביניהן גבוה, תהליך הקורוזיה יתרחש במהירות.
דוגמה לשילוב שגוי בין חומרים: אלומיניום ונירוסטה. דוגמה לשילוב נכון של חומרים: אלומיניום ואלומיניום.
*אם בכל זאת נדרש להשתמש בשתי מתכות הרחוקות אחת מהשניה בשורה הגלוונית, יש לבודד ביניהן (ציפוי, אטם, וכו').
הערה: *ישנם סוגים נוספים של קורוזיות.
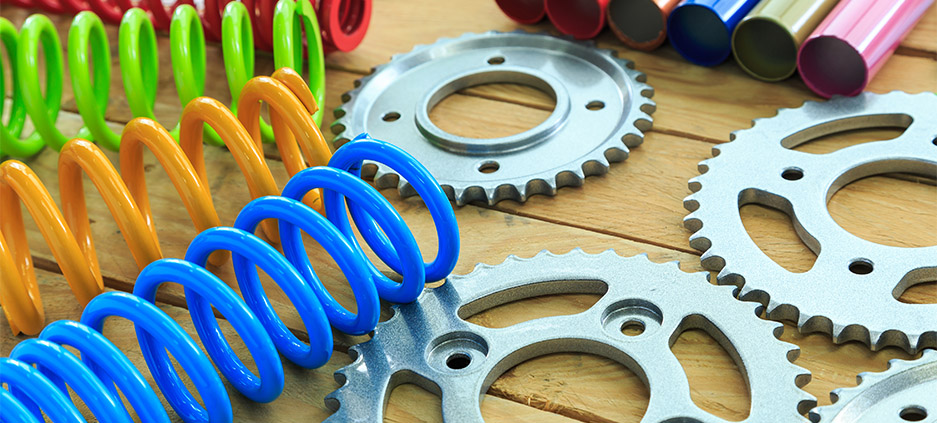
סדר הפעולות הנדרשות לטובת ביצוע תהליך הצביעה או הציפוי:
1. הכנת השטח – צביעה / ציפוי
זהו שלב חובה הנדרש לפני ביצוע תהליך צביעה או ציפוי. בתהליך זה מבצעים הסרת שומנים או חלודה. תהליך זה הינו קריטי וחייב להתבצע בכדי להבטיח הדבקות (אדהזיה) מיטבית של הצבע או הציפוי למשטח.
1.1. דרכי הטיפול הנפוצות להסרת שומנים:
1.1.1. ניקוי בממיס שומן. (Solvent)
1.1.2. ניקוי באדים (דגריזר). (Vapor spray degreaser)
1.1.3. ניקוי בחומרים סבוניים (אלקלי) (Alkali)
1.1.4. ניקוי אולטרסוני (Ultrasonic cleaning)
1.2. דרכי הטיפול הנפוצות להסרת חלודה:
1.2.1. ניקוי מכני ידני – ניקוי פני השטח באמצעות כלים ידניים כגון צמר פלדה או מברשת פלדה. תהליך זה אינו מתאים לטיפול פני שטח מסוג אלומיניום. זאת מפני שהפלדה עלולה ל"היתקע" באלומיניום ולגרום לקורוזיה. (ראה הגדרת קורוזיה גלוונית).
1.2.2. ניקוי אברזיבי -(Abrasive blasting) הידוע בכינוי "ניקוי חול", הינו תהליך ניקוי פני שטח באמצעות התזה של חומרים מתכתיים ("קשים") או אורגניים כגון חול ("רכים"). שימוש בחומרי התזה קשים מוריד מעובי החומר המטופל, ובהתאם תהליך זה מיועד לטיפול במתכות. שימוש בחומרי התזה רכים מיועדים לטיפול בחומרים מרוכבים (פלסטיק ועוד). כיום מטעמי בטיחות בסביבת עבודה, כבר לא נהוג להשתמש בחול, אלא בחומרים אורגניים חלופיים כגון קליפות אגוז, גרגרי תירס וכו'. זאת מפני שהחול כולל סיליקון אשר עלול להיות רעיל ולהזיק לבריאות בעת שאיפתו.
• תקן A-A-59316 מפרט סוגים וגודל של גרגרים מומלצים. רמת החספוס בתהליך ההתזה (ניקוי אברזיבי) נקבעת ע"י גודל החלקיקים ומהירות ההתזה.
1.2.3. טיפול בחומצה.
1.3. חשוב לדעת!
תקנים רלוונטיים: (ISO)
8501 – בדיקה ויזואלית של ניקיון פני השטח.
8502 – בדיקות לניקיון פני השטח.
8503 – אפיון חספוס פני השטח.
8504 – שיטות להכנת פני השטח.
TT-C-490 – תקן להכנת שטח.
2. תהליך היישום – צביעה (Paint )
2.1. פירוט מרכיבי הצבע:
2.1.1. חומר מקשר (שרף) (Binder):
החומר המקשר אחראי על ההדבקות (אדהזיה/adhesion) ויצירת שכבה (כרום/film) אחידה על פני השטח של חומר הגלם המטופל. בנוסף, מרכיב זה תורם לקשיות ועמידות הצבע.
החומר המקשר הינו שקוף ובעל ברק ביסוד שלו. תכונות אלו משתנות לאחר הוספת הפיגמנט (סעיף 2.1.2). רמת הברק (gloss) של שכבת הצבע הסופית תלויה ביחס שבין החומר המקשר לפיגמנט (נפח יחסי). שכבת צבע עם רמת ברק גבוהה, תכלול אחוז נמוך של פיגמנט ותהיה בעלת עמידות נמוכה לשחיקה יגימור בעל תכונות אלו נקרא גימור מבריק (glossy).
שכבת צבע עם רמת ברק נמוכה, תכלול אחוז גבוה של פיגמנט ועמידות לשחיקה גבוהה יחסית. גימור בעל תכונות אלו נקרא גימור מט (matt).
תקריב של שתי האופציות, יציג שכבת צבע עם פני שטח מחוספסים במקרה של גימור מט, ובמקרה של גימור מבריק פני השטח יהיו חלקים.
2.1.2. פיגמנטים (Pigments):
חומר אבקתי אשר אחראי על הגוון, והאיטום של שכבת הצבע הסופית. מטרת האיטום היא הגנה מפני קרינת השמש שפוגעת בשכבת הצבע לאורך זמן. בעבר היו עושים שימוש בפגמנטים מסוג אבץ, כרומט או עופרת למניעת קורוזיה. אך לאחר שנאסרו לשימוש לפי תקן ROHS, השימוש בהם הופסק. קיימים פיגמנטים עם תכונות נוספות כגון החזר אור (זוהר) ומוליכות.
2.1.3. מדלל (ממיס) (Solvents)
אחראי על כך שתערובת הצבע לא תתקשה, על מנת שניתן יהיה לערבב אותה. בהתאם, תהליך נידוף המדלל מתערבות הצבע, חיוני להתקשות הצבע על פני השטח של חומר הגלם. אי לכך, לטובת זירוז תהליך נידוף המדלל ("ייבוש הצבע") נעשה שימוש בחימום אשר מקצר את משך ההתנדפות של המדלל. שאיפה של חומר מדלל מזיקה לבריאות ויש להתמגן בהתאם. ניתן למדוד את הרעילות של המדלל לפי הסוג שלו.
2.1.4. תוספים
חומרים המשפרים את תכונות הצבע בהתאם ליעוד שלו. תוספים אלו יכולים להאריך את אורך החיים של התערובת (לפני ההתקשות), להאיץ את תהליך ההתקשות / ייבוש, לבלוע אור ולהגן מפני קרינה מייננת, לשפר מוצקות, לאפשר גמישות ועוד.
2.2. תהליך הצביעה:
תהליך הצביעה נחלק לשני סוגים עקריים:
2.2.1. צביעה רטובה – ריסוס של תערובת נוזלית על מגוון חומרי גלם.
לשיטת זו מספר יתרונות:
• ניתן ליישם של מספר שכבות צבע כמעט ללא הגבלה.
• חדירה לפני שטח בעלי גאוטריה מורכבת.
• לא נדרש ציוד כבד (ניידות גבוהה) ולכן ניתן צביעה בשטח.
• קיים מבחר גדול של חומרים מקשרים (שרפים) וציוד הצביעה זול יחסית.
החסרונות של שיטה זו:
• הם זמני צביעה ארוכים.
• לא ניתן למחזר את התערובת.
• המדללים עלולים לסכן את המשתמש ולפגוע באיכות הסביבה.
2.2.2. צביעה באבקה – ריסוס של אבקת צבע הנצמדת לחומר הגלם ע"י מטען חשמלי (אלקטרוסטטי), והופכת לשכבת צבע אחידה וקשה ע"י חימום בתנור.
לשיטת זו יתרונות כגון:
• לא מבוצע שימוש במדלל.
• ניתן למחזר את החומר שלא יושם על האובייקט הנצבע.
• זמני צביעה קצרים.
החסרונות של שיטה זו:
• עלות מתקן הצביעה גבוהה.
• מספר שכבות מוגבל.
• האלמנט הנצבע צריך להיות עמיד בחום.
הערה: כל הגוונים מיוצגים ע"י תקן גרמני RAL-840 או ע"י תקן אמריקאי STD595.
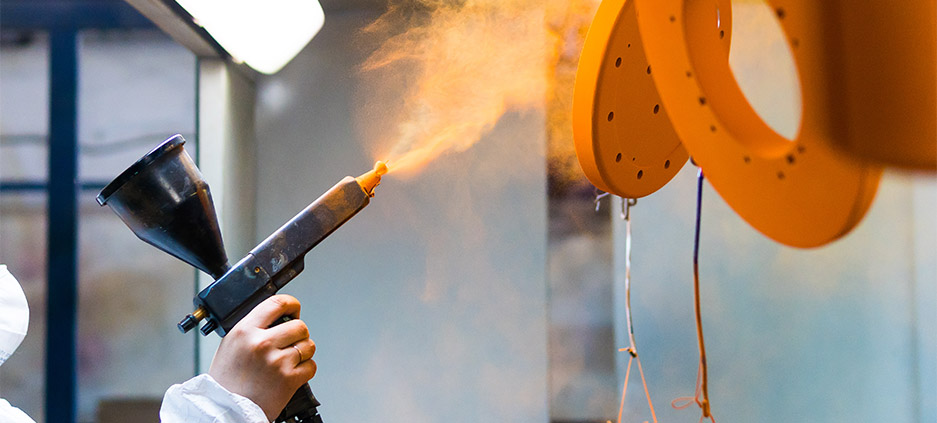
3. תהליך היישום – ציפוי חשמלי (Elctroplating process)
3.1. הרכב ויישום תהליך הציפוי:
תהליך הציפוי כולל שלושה שלבים עיקריים:
3.1.1. שלב הניקוי והצריבה
3.1.1.1. תהליכי הכנת השטח לציפוי – ראה סעיף 1.
3.1.2. מרכיבי תהליך הציפוי (תהליך עקרי)
3.1.2.1. טבילת חומר הגלם בתמיסה מיימית של יוני מתכת וכימיקלים נוספים – אלקטרוליט (Electrolyte).
3.1.2.2. מישר זרם (Rectifier) – מספק זרם ישר לאלקטרודות (האנודה/קטודה) הטבולת בתוך התמיסה המיימית.
3.1.2.3. בתהליך החשמלי, החומר המצפה ממנו מורכבת האנודה (קוטב חיובי) מתמוסס ועובר לקדוטה (קוטב שלילי) שהיא למעשה מתקן דפינה עליו תלוי חומר הגלם. ובעצם תהליך מצופה חומר הגלם שהתמוסס מהאנודה.
*קיימים שני מתקני דפינה נפוצים:
מתקן דפינה בתליה – מחובר לקטודה. צורת התליה, משפיעים על איכות הציפוי. תליה לא תקינה או מתקן לא מתאים, עלולים להשאיר אוויר לכוד או לגרום לייבוש לא מיטבי של החלק המצופה.
מתקן דפינה מסוג תוף (Barrel)- משמש עבור חלקים קטנים. מעטפת התוף משמשת כקטודה ויוצרת מגע בין החלקים לתוף ולתמיסה.
3.1.2.4. עובי הציפוי:
הציפוי בתהליך זה אינו מתפזר בצורה אחידה על פני השטח של חומר הגלם. העובי תלוי במספר פרמטרים, כגון: טמפרטות התמיסה, עוצמת הזרם, משך הטבילה וגאומטרית האלמנט המצופה. בתהליך התכן של פריט אשר עתיד לעבור ציפוי, יש להתחשב בגיאומטריה שלו. לדוגמה, קיים קושי בחדירת הציפוי לפינות חדות, או הצטברות ציפוי עבה בפינות.
3.1.3. טיפול גמר:
3.1.3.1. שטיפת חומר הגלם במים.
3.1.3.2. ייבוש של כל שטח הפנים של חומר הגלם, בדגש על גאומטריות בעיותיות שנוזל יכול להאגר בהם ולגרום להתפתחות של קורוזיה. יש להשתדל להמנע מחללים פנימיים (סגורים) בתהליך התכן של הפריט, או להשתמש בקדחים עוברים ונקודות ניקוז.
3.1.3.3. אריזה ואחסון – חשוב להקפיד על אריזה שמגנה מפני פגיעות ושריטות, כי בנקודות האלה הלחות יכולה "לתקוף" את החלק המצופה ועלולה להתפתח קורוזיה.
3.2. ציפויים נפוצים
3.2.1. אבץ – ציפוי בתהליך חשמלי בטבילה בתוך אלקרוליט
הציפוי נותן עמידות בפני קורוזיה ומשמש כשכבה דקורטיבית.
מיושם בעוביים הנעים בין 5 ל-25 מיקרון. לציפוי זה מספר גוונים שונים: שחור, ירוק, צהוב, טבעי – הגימור (פסיבציה וגוון) מוגדר ע"י ה- Type, (Type V ו-Type Vl תואמי תקן RoHS.
3.2.2. אלקטרולס ניקל – ציפוי בתהליך טבילה בתמיסה – כימי (לא חשמלי)
הציפוי נותן עמידות בפני קורוזיה ומשמש כשכבה דקורטיבית.
היתרונות של ציפוי זה הן: עובי ציפוי אחיד גם בגאומטריות מסובכות, קושי גבוה (לאחר טיפול תרמי), עמידות גבוהה בשחיקה וניתן ליישם את הציפוי גם על "אל מתכות".
מיושם בעוביים הנעים בין 0.1 ל-75 מיקרון – הגדרת Service Conditions (SC).
הדרישה לטיפול תרמי (משך וטמפרטורה) נקבעת ע"י הגדרת CLASS.
3.2.3. אלודיין – טיפול תמורה לאלומיניום
הציפוי בעל גוון צהוב / זהוב או שקוף, משמש להגנה מפני קורוזיה והולכה חשמלית משופרת (התנגדות נמוכה). בנוסף הציפוי מהווה בסיס טוב לצביעה.
אופי הציפוי והיחס בין עמידות לקורוזיה לבין הולכה חשמלית נקבע ע"י הגדרת CLASS.
בתהליך ציפוי מסוג זה יש להתשמש בהגדרת Type II בלבד, אשר תואמת את תקן RoHS.
3.2.4. אנודייז – ציפוי בתהליך חשמלי בטבילה בתוך אלקרוליט (שונה מתהליך ציפוי האבץ)
הציפוי בעל עמידות גבוהה בשחיקה – קשיות גבוהה, הגנה טובה מפני קורוזיה ובידוד חשמלי.
בתהליך זה, הציפוי הופך להיות חלק מהאלמנט המצופה, ע"י חדירה של חלק מהציפוי לתוף השכבה העליונה של האלמנט. באנודייז רגיל כ-66% מהציפוי חודר וכ-34% נותר חיצוני, באנודייז קשה 50% מהציפוי חודר, ו50% נותר חיצוני. בעת הסרת הציפוי עובי החומר קטן – ההסרה תוריד מעובי החומר ביחד עם הציפוי שחדר. עובי הציפוי נע בין 2 ל-80 מיקרון. עובי אנודייז רגיל נע בין 2 ל-25 מיקרון, לעומת זאת העובי של אנודייז קשה נע בין 40 ל-80 מיקרון.
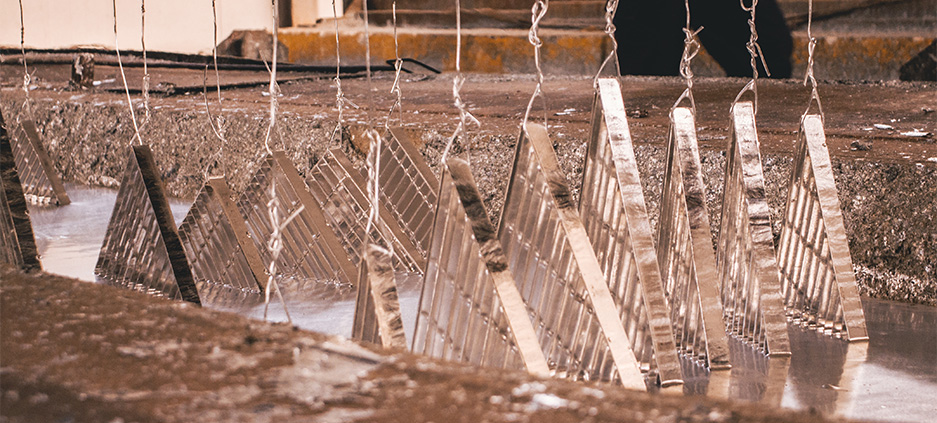
4. בדיקת אדהזיה
מתבצעת ע"י בדיקה הרסנית – בדיקה מסוג זה פוגעת בתכונות הפריט ולא ניתן להשתמש בו כיוון שלא תואם את דרישות המפרט יותר. לדוגמה, אחת הבדיקות הנפוצות היא באמצעות סכין ונייר דבק. מתבצעת פעולת חיתוך באופן מסוים של הפריט הצבוע או המצופה, ואז מדביקים את נייר הדבק לאזור שנחתך. לאחר שמסירים את נייר הדבק ניתן להעריך את טיב האדהזיה לפי כמות הצבע או הציפוי שנשארה "דבוקה" לחומר הגלם. (Adhesion test / Pull off test), בבדיקה זו יכולים להתגלות שני סוגי כשלים:
1. כשל בין הצבע / הציפוי לחומר הגלם.
2. כשל בין מרכיבי הצבע / טיב הציפוי.
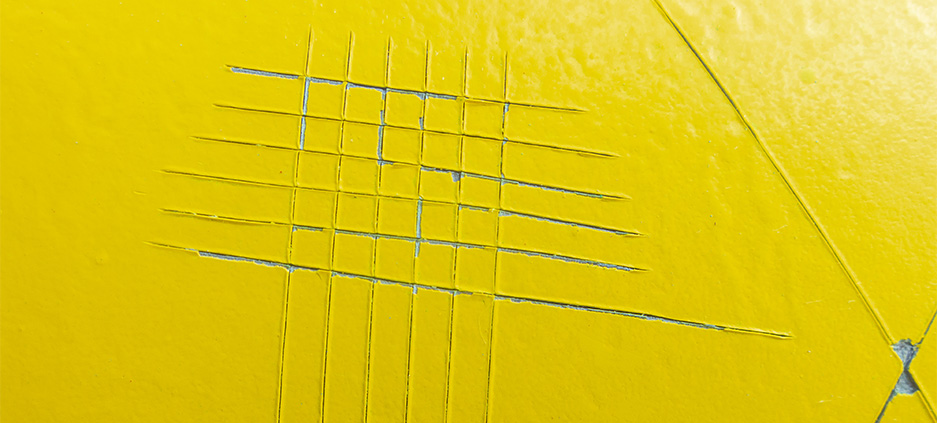
התקנים לבדיקות אדהזיה הם: ASTM D 4541 ו- ASTM-D-3359.
הבדיקה מתבצעת על יחידה אחת מתוך מנת ייצור. כיוון שהבדיקה היא בדיקה הרסנית, נהוג לייצר בכל מנה "בול צבע" מלווה. זוהי פלטה פשוטה אשר נצבעת או מצופה ביחד עם מנת הייצור, באותם התנאים והיא תשמש לבדיקת האדהזיה.
עמידות הצבע / ציפוי תלויה מאד בסוג הכנת השטח.
לדוגמה, עבור צבע יסוד וצבע עליון בעובי של 0.045 מ"מ אשר הכנת השטח שבוצעה היא ניקוי אברזיבי, אורך החיים עד להופעת קורוזיה יהיה קצת מעל 6 שנים. עבור אותו עובי צבע, והכנה בחומצה, אורך החיים יהיה 4.5 שנים, וניקוי במברשת פלדה יעניק אורך חיים של קצת מעל שנה.
*הסטטיסטיקה לכשל הצבע (לפי נתוני NACE & SSPC) מתפלגת כך שכ-70% מהכשלים נגרמו ע"י הכנת שטח או יישום לקויים,כ-20% מהכשלים נגרמו בעקבות מפרט לא תקין, ושאר הכשלים, כ-10% בעקבות חומר פגום.
הערה
מאמר זה סוקר את הסוגים והתהליכים הנפוצים בתעשיית הצבע והציפויים. קיימים סוגים ותהליכים נוספים, ובצוק מערכות קיים הידע ויכולת התמיכה באותם תהליכים.